New in Fall 2022! The IC can now cut standard-sized business cards! Students can submit one business card (front and back), and let us know how many they need. The Imaging Center can gang them up on a larger sheet and cut them with a machine so they are exact.
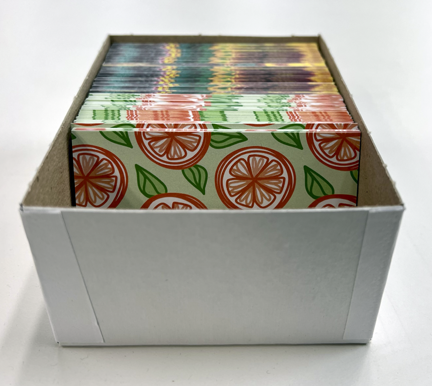
The business card template is available for download under our template page. This template allows the IC to do the heavy lifting and cut the cards for you!
There is an added charge of $3 dollars (fall 2022 pricing) for this service. There is not currently a print minimum, subject to change. If you order more than 240 cards or more, we will box them up for you for no additional charge.
The Process
The IC has created a standard-sized business card template that allows us to cut your business cards. In order to have your order cut, we require your full cooperation to prepare the file correctly. The IC is not liable for reprints if you fail to follow any of these directions.
Our InDesign template is specific to the way that the IC process, prints, and applies the cutting to your order.
Using a template downloaded from another website will not work. This particular InDesign template is fine-tuned to the millimeter to work with our printing software and cutting machine.
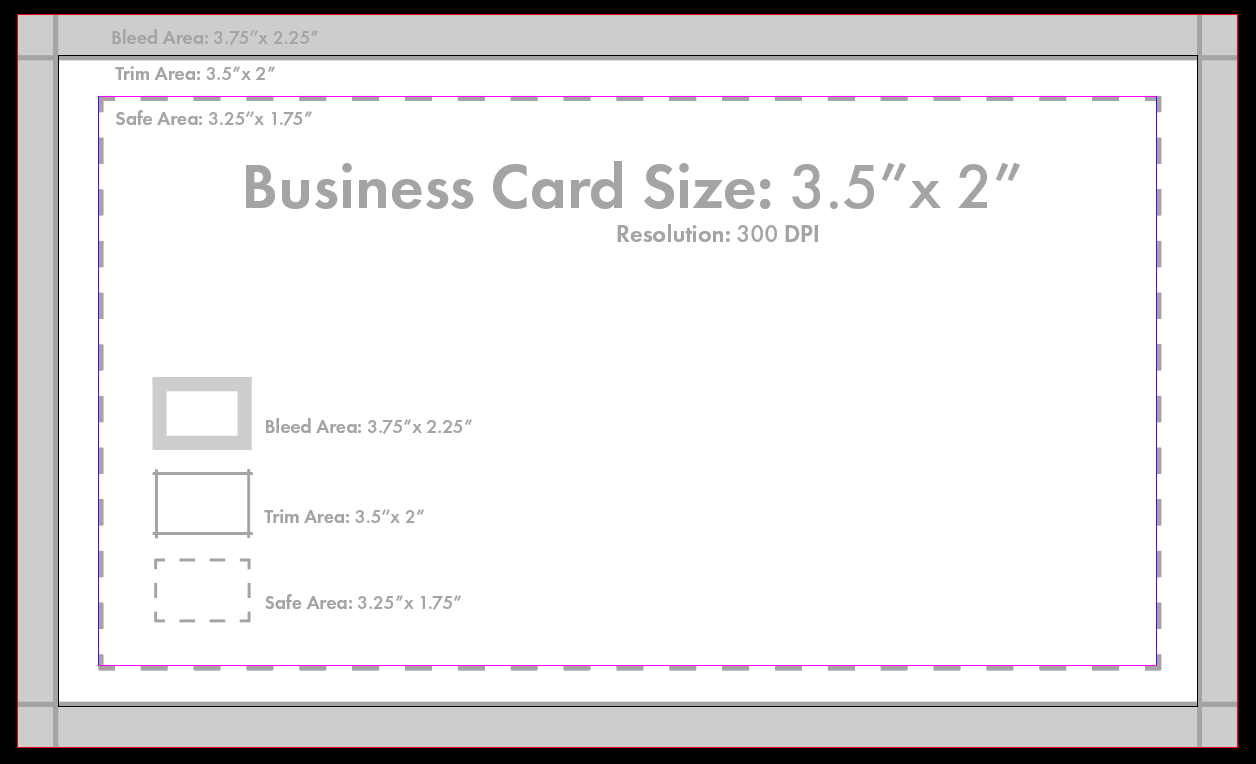
Standard Card: 3.5″ x 2.0″
Final PDF size: 3.75″ x 2.25″
Bleed Area: 3.75″ x 2.25″
Trim Area: 3.5″ x 2.0″
Safe Area: 3.25″ x 1.75″
Your print & cutting job will be completed in the order it was received. The standard turnaround time for printing & cutting is 48 hours (two full business days). There are no “Rush” options. Please be aware that during midterms and finals, turnaround times can increase up to 2-3 business days.
For example, if you submit a business card request at 6:00 pm on a Monday, the earliest you will receive the finished cut business cards, will be approximately 10:00 am on a Wednesday.
Design/Artwork Guidelines
Make sure your text is inside the safe area.
The “safe area” is designated using margins in our InDesign template and is shown by the purple/pink line. By putting text or design elements past this “safe” line, you run the risk of it being cut off or appearing too close to the edge of your business card.
Make sure that your image is full bleed.
If you have design elements that extend to the cut line, be sure that you extend them past the black cut line and all the way to the purple/pink bleed line to ensure that there is absolutely no white border on your trimmed business card.
Make sure that your business card is the correct size & resolution.
Confirm that your design is the correct size. This template will have a final size that is 3.75″ x 2.25″.
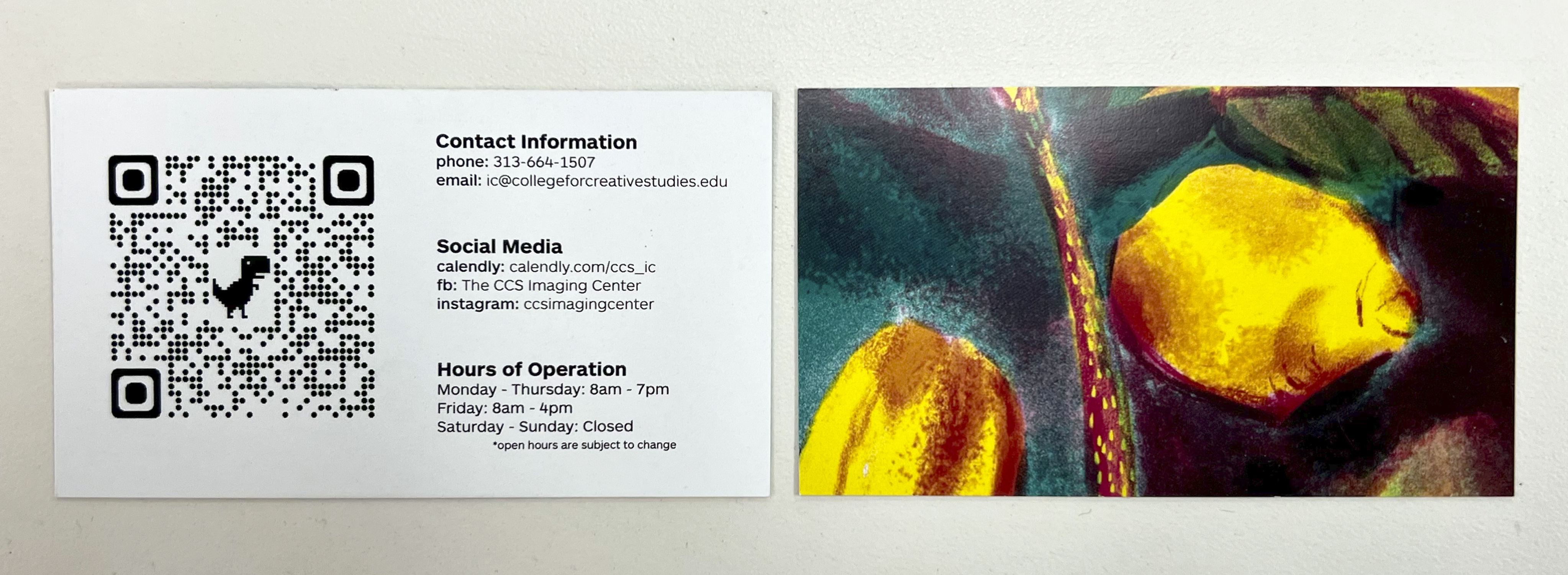